TOUCH AND FEEL AT THE NANOSCALE
PRODUCTS
Self-Sensing Cantilever Probes
Silicon piezo-resistive self-sensing cantilevers enable complete new applications in the fields of Atomic Force Microscopy (AFM), nanoprobing, torque-magnetometry, or other sensing applications such as gas dynamics and media properties.
These cantilevers exhibit an integrated piezo-resistive Wheatstone bridge which directly measures the cantilever deflection electrically. This readout technique removes the space-consuming optical laser readout needed before.
Self-sensing technology enables an easy and seamless integration with various instruments (e.g. SEM, TEM, but also many other measurement systems). The cantilever chip is bonded onto a small PCB with a small connector for a quick cantilever exchange.
Standard SCL self-sensing cantilevers exhibit a tip with a tip radius smaller than 15 nm and are available with a variety of resonance frequencies and spring constants. Tipless and long-life SCD-tip cantilevers are available, too.
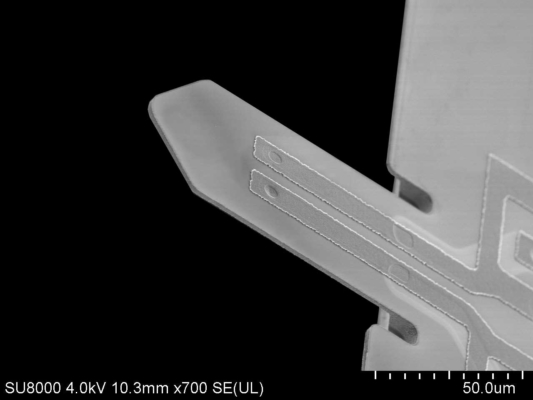
Self-Sensing Tipless Cantilevers
Self-sensing cantilevers without tip for various applications like highly sensitive gas detection, torque magnetometry, force sensing, etc.
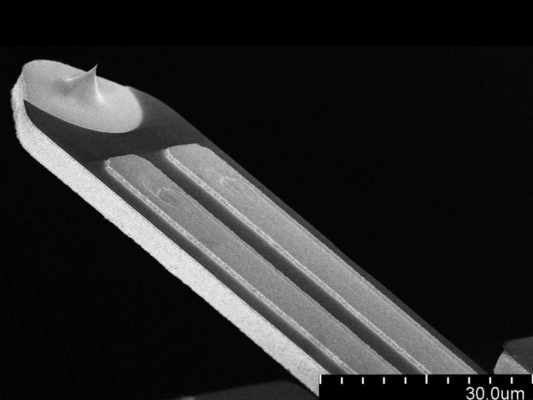
Self-Sensing Si-Tip Cantilevers
Standard self-sensing cantilevers with a sharp silicon tip for AFM microscopy, force sensing, etc. in contact or non-contact mode.
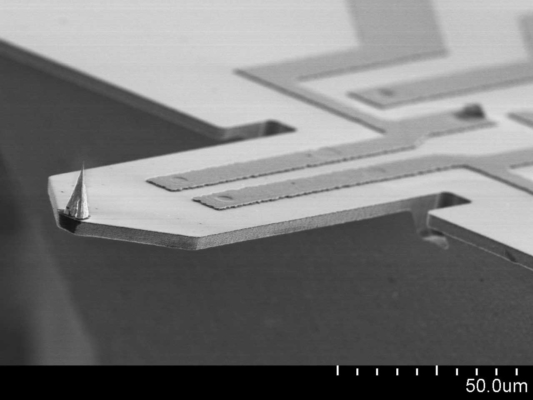
Self-Sensing SCD-Tip Cantilevers
Self-Sensing cantilevers with a hard and long-life single crystal diamond tip for AFM, high aspect ratio samples, etc.
TRILAYER MEMS CANTILEVER TECHNOLOGY
New “self-sensing” cantilever with integrated electronic and actuation mechanisms
Integrating electronic and actuation mechanisms into micromechanical devices such as MEMS cantilevers are widely used to transduce an applied force to an electrically measurable signal. Employing such “self-sensing” cantilever in an atomic force microscope (AFM) allows getting ride of the optical read-out by a laser reflected at the backside of the cantilever. This opens new applications where there is not enough space for the optical read-out module above the sample to be investigated or where the sample has to be immersed into – even – nontransparent liquids like for biological samples.
In most of the traditional AFMs, the deflection of the cantilever is detected using the optical beam deflection method where a laser beam reflected from the back of a cantilever is centered on a quadrant photo diode. An alternative is measuring the cantilever bending by integrated piezo-resistive sensors. A high sensitivity is achieved by measuring the resistance of the sensors by means of a Wheatstone bridge.
The deflection sensitivity of the self-sensing cantilever increases with its thickness due to the increased distance of the sensors from the neutral axis of the cantilever. However, the spring constant of the cantilever increases strongly with its thickness.
The design of these new cantilevers incorporates an elastically soft polymer core enveloped by 2 hard thin film layers. This patented new cantilever concept provides additional degrees of freedom to optimize the performance of the MEMS cantilever. The
most striking advantages compared to standard Si or SiN self-sensing cantilever are:
-
For a given resonance frequency f0, the force sensitivity of the trilayer is up to 10 times higher than that for silicon cantilevers.
-
The use of a polymer as core of the AFM cantilever increases its bandwidth f0/Q, – Q is the mechanical quality factor. This is particularly advantageous when imaging in vacuum when fluid of air damping is absent. Excellent resolution can be achieved even at imaging speeds up to 10 times higher than with Si or SiN self-sensing cantilever.
-
All sensing elements and electrical connections are hermetically sealed inside the MEMS device, which makes the trilayer devices inherently suited for measurements in fluids – even in opaque, electrically conductive or harsh chemical environments.
The trilayer technology is not limited to self-sensing cantilevers. Examples are fluid-compatible membrane-type surface-stress sensors or force-sensors with resolution in the nN-range.
For a detailed description see “A hybrid polymer / ceramic / semiconductor fabrication Platform for high-sensitivity fluid-compatible MEMS devices with sealed integrated electronics” by Nahid Hosseini et al. (arxiv_2307.05221)
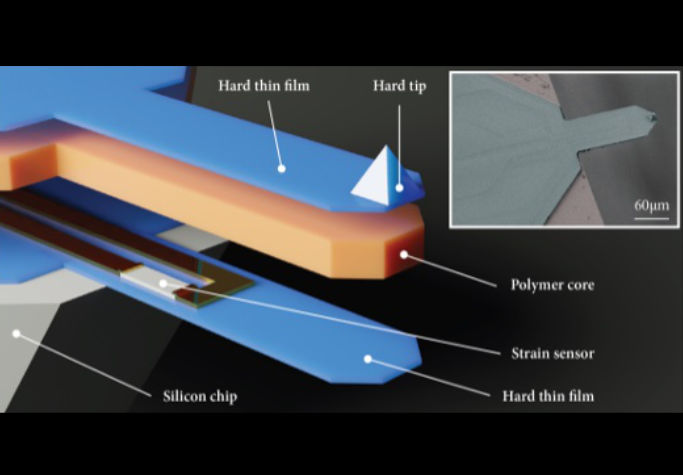
Standard TriLayer Cantilevers
Self-sensing Trilayer Cantilevers feature a unique structure with Silicon Nitride films and a polymer core – available in different dimensions and with and without tip.

KPFM / c-AFM Trilayer Cantilevers
Self-sensing Trilayer Cantilevers featuring conductive coating for easy use in KPFM or c-AFM measurements.

Quantum Twisting Microscopy (QTM) Trilayer Cantilever
Tip-less Trilayer Cantilever with additional Pt-Traces connecting to the tip for easy use in Quantum Twisting Microscopy (QTM) experiments. Available with 2, 4, or 6-Pt-Traces.
CUSTOMIZED CANTILEVER SENSORS
In order to guarantee the greatest possible flexibility for individual problems of our customers, c-sense offers customized cantilevers. We are also open to potential new cantilever developments. Do not hesitate to contact us.
STARTER KIT
Self-Sensing Starter Kit
The Self-Sensing Starter Kit includes a pre-amplifier, connection cables and 10 pieces of cantilevers to get easily started. The core element of c-sense self-sensing starter kit is the pre-amplifier. It supplies a Wheatstone bridge based sensor with a stable and low noise reference voltage and amplifies the bridge output signal.
Contact us:
This site is protected by reCAPTCHA and the Google Privacy Policy and Terms of Service apply.